FloridaGreen® encompasses two technologies: Greenhouse Technology with Solar Thermal Pasteurization
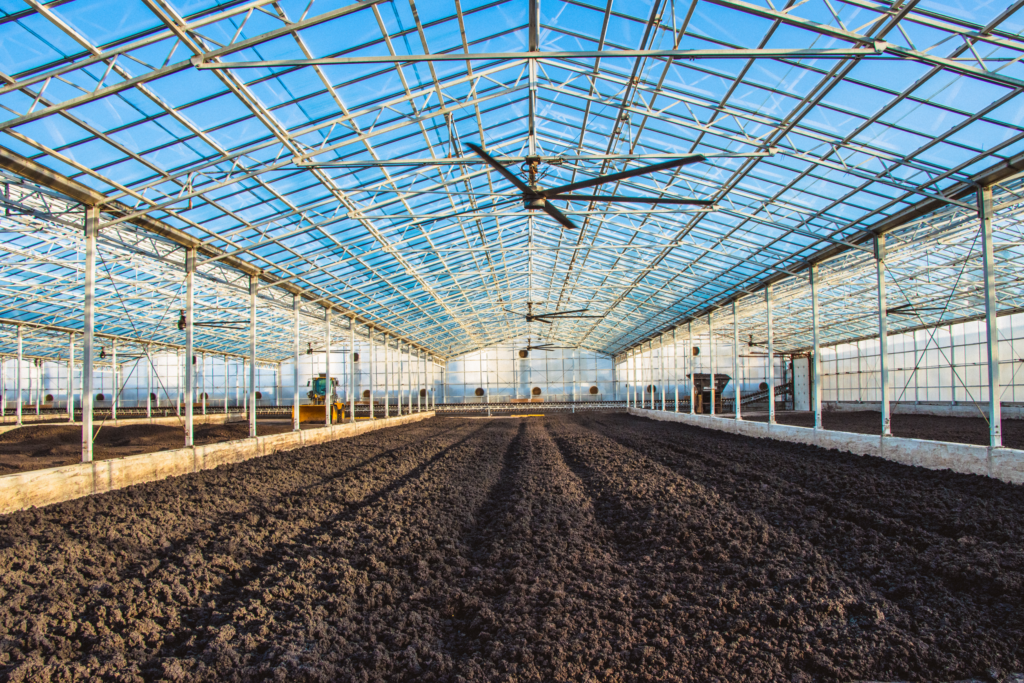
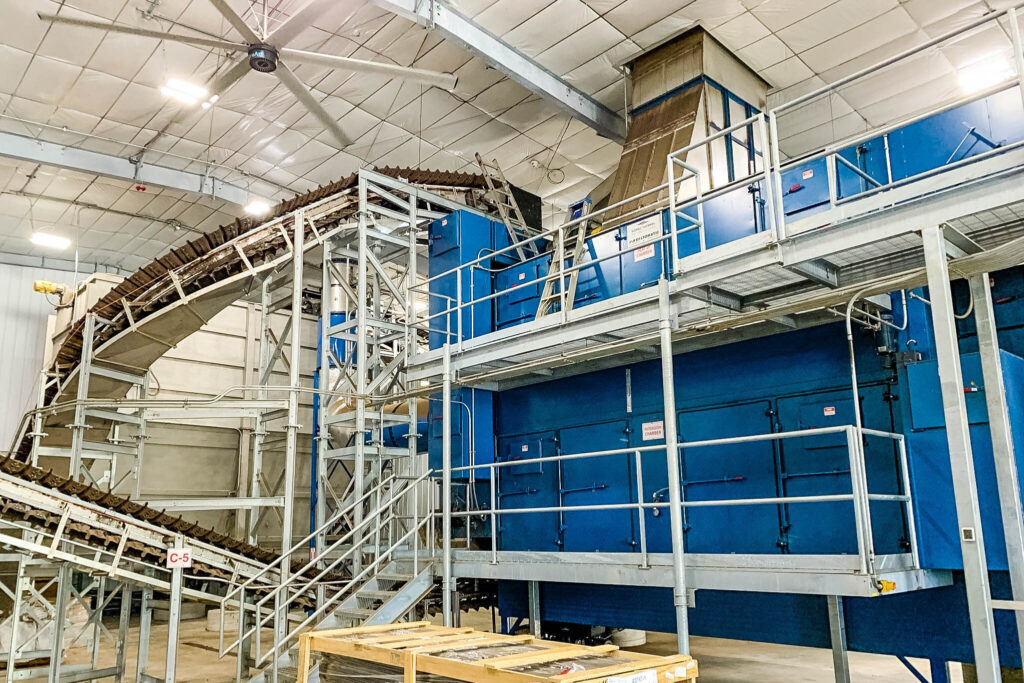
Greenhouse Technology
Greenhouses are effective in removing moisture from biosolids when conditions are controlled. To control the conditions, we fully enclosed our greenhouses (also called pods) and placed ceiling fans inside to stir the air. Each of our pods is about an acre and a third. The fans enhance the evaporation effect of the biosolids.
We also have activated carbon systems in our greenhouses that are doing two things.
1. Removing odor and cleaning the air
2. Removing moisture
In order to make our greenhouses safe to work in from a labor standpoint, we needed to have 6 exchange rates per hour, according to the NFPA 820 code. FloridaGreen has 12 exchange rates per hour — which means every 5 minutes, we are exchanging air in the greenhouses.
As we dry the material, we lay it across the floor in the greenhouses and we agitate the material with a tractor and a rotary tiller. The rotary tiller takes the dry, crusted material on the surface and rolls it underneath the wetter, moister material. We stir the biosolids 3-4 times a day. As the biosolids are drying, we are reducing the volume in the greenhouses. Our target dryness is 60% solids. By the time we reach our goal of 60% solids, we have reduced the original volume down by about 33%.
Solar Thermal Pasteurization
The material is transferred from the greenhouses to our processing building with a belt conveyor system. It drops into a stainless-steel hopper. From the hopper, it is conveyed to the top of the oven to begin the process of pasteurization. Material is placed on the top oven belt, called the “Heat Up Chamber.”
The Heat Up Chamber has 3 inches of material placed on the belt and 30,000 CFM of hot air is forced through the material. This heated air begins the drying process and brings the material up to pasteurization temperature of 70 degrees Celius or 158 degrees Fahrenheit prior to dropping on the lower belt.
As the material reaches the end of the Heat Up Chamber, we have two options:
1. Reach Temperature at the End of the Belt
2. Reach Temperature Halfway & Increase Belt Speed
Making the transition to the lower pasteurization chamber, has a similar approach to the Heat Up Chamber. The difference is the belt speed will not go faster than 30 minutes from placement to discharge. This allows us to ensure the material reaches pasteurization requirements. Throughout the belt, temperature probes are reading the internal temperature of the material, ensuring it is above 158 degrees Fahrenheit. Upon reaching the end of the belt, material is discharged on a conveyor belt, transferring pasteurized material to a covered fertilizer bunker. In this bunker we have the option to load directly into a trailer or store material for up to 21 days.
Pelletization Process
Following pasteurization of biosolids, the material is very inconsistent in size/shape. Pelletizing forms the biosolids into an easy spreading fertilizer for homeowners and farmers. The process starts with the biosolids being conveyed into the top pellet chamber, where rollers force the biosolids through the pellet die holes. On the underside of the die, blades cut the pellets to length. This process generates a lot of heat from the friction caused from the rollers contact to the die. Two-hundred degree Fahrenheit pellets are discharged on a screening table to remove any dust or oversized material. The pellets are transferred to a cooler where they spend 10-12 minutes under a blower to prevent them from self-combusting. Once the pellets are cooled, they are conveyed to the bagging equipment, where they are bagged, pelletized, and stored in a warehouse until being shipped to a retail store.
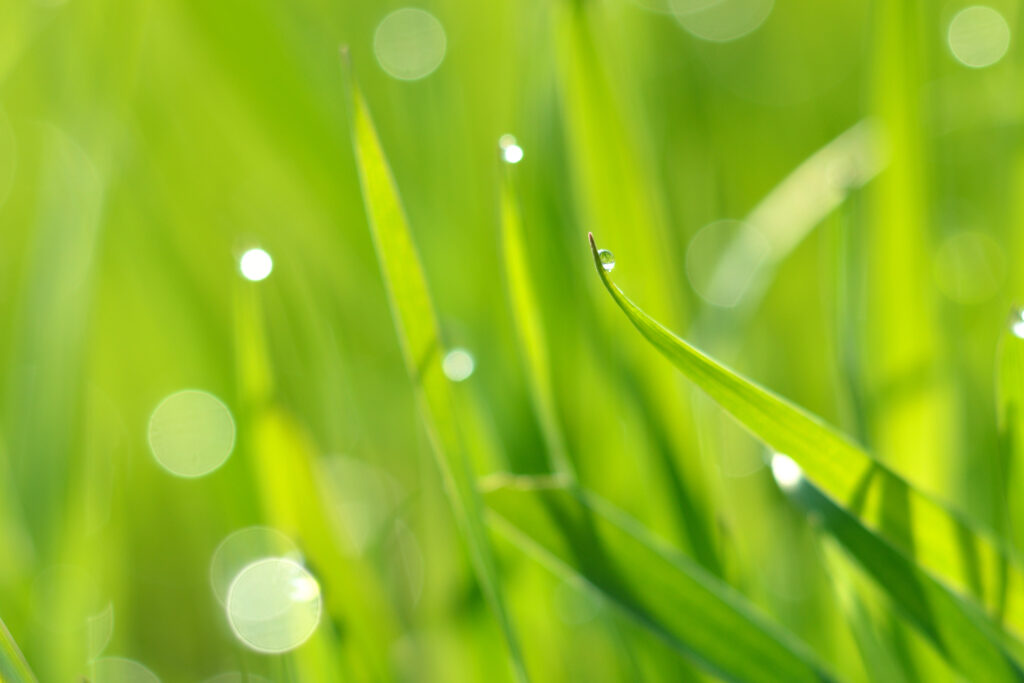
Why Pelletize?
When Class A, exceptional quality (EQ) biosolids are produced using a drying or thermal process, the end product can often contain varying amounts of dust. A dusty product can create issues related to uneven spreading patterns, drifting and improper nutrient placement.
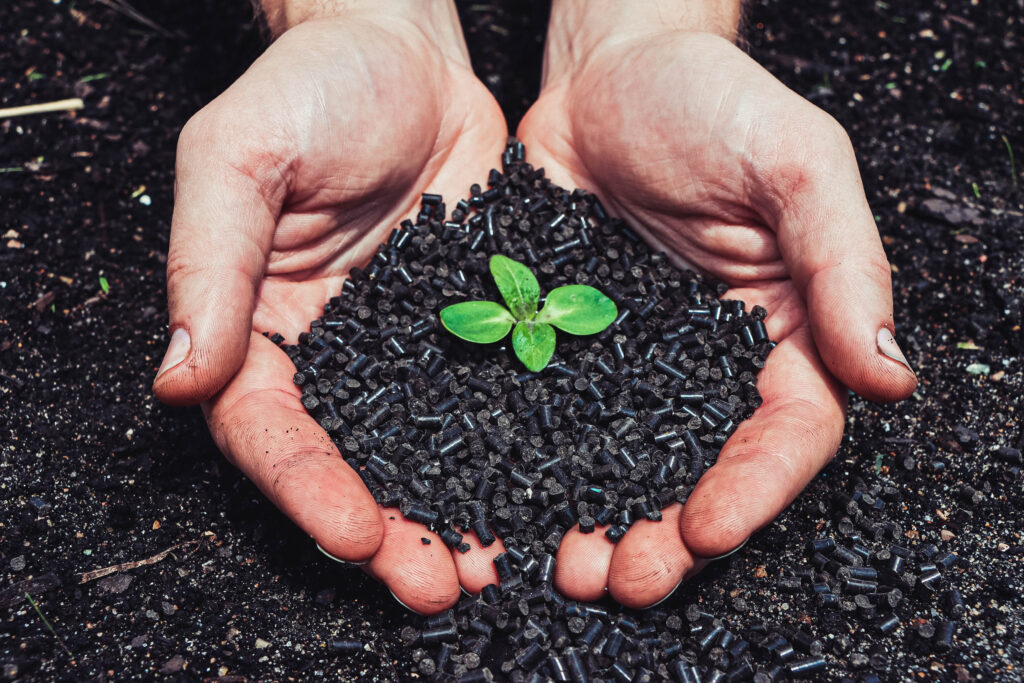
How Does Pelletization Happen?
When biosolid fertilizer is pressed through specially designed die plates, the friction of the process produces heat. At the proper temperature, the naturally occurring lignen in the biosolids is released to help in the formation of the pellet. Lignen is a complex organic polymer found in the tissue of most plants, therefore it is naturally present in biosolids.